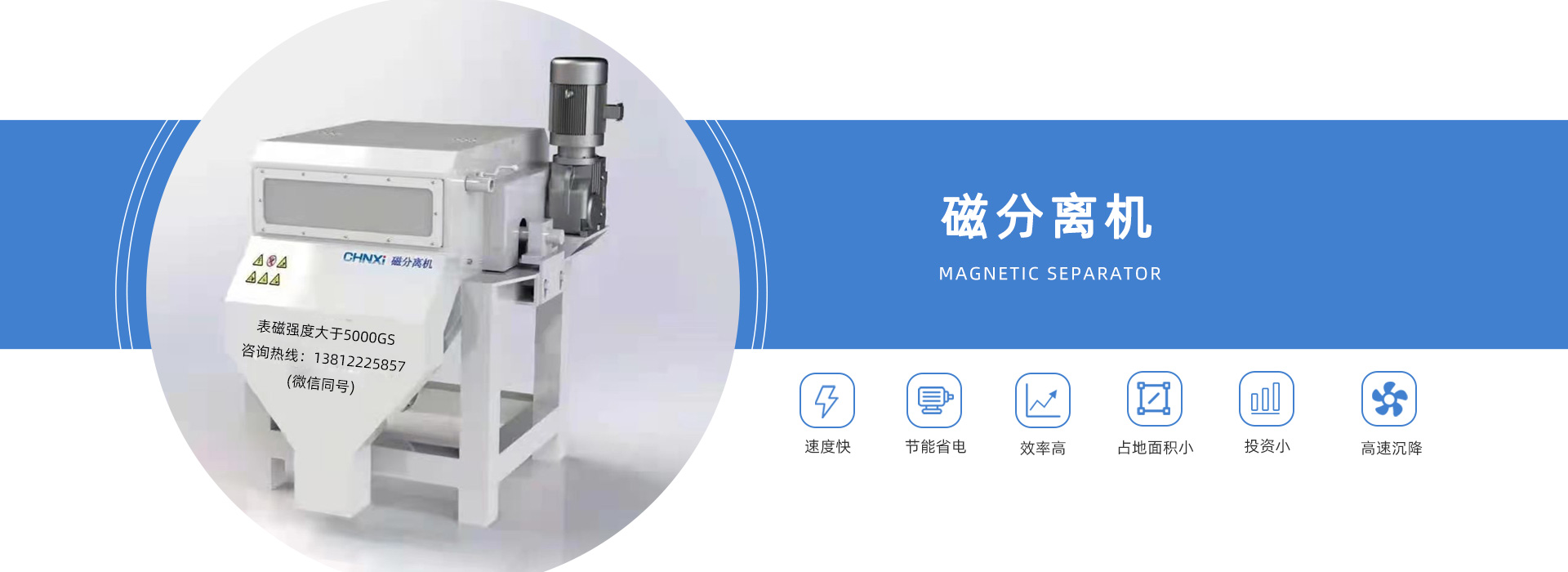
集團動態(tài) News Information
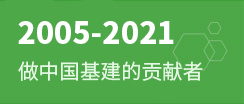
怎么預防混凝土堵泵堵管呢?很多朋友都做錯了!
隨著商品混凝土的推廣應用,采用輸送泵進行混凝土的運送,大大地提高了混凝土的施工效率和機械化水平,這種施工技術被廣泛地應用于橋梁、公路、水利、樓宇等建筑的施工。
用于泵送的混凝土必須符合《混凝土泵送施工技術規(guī)程》JGJ/T10,不適宜泵送的混凝土將加劇泵機的磨損,降低施工效率,造成資源的浪費。堵泵現(xiàn)象是我們不愿看到的,那么如何來預防混凝土輸送過程中的堵泵、堵管現(xiàn)象呢?現(xiàn)就以下幾點原因加以分析:
1.1混凝土的和易性
混凝土的和易性直接反映了混凝土的泵送性能,混凝土的可泵性一般用10s時的相對泌水率S10(不宜超過40%)來表示。
混凝土在泵送過程中的輸送阻力隨著坍落度的增加而減小。泵送混凝土的坍落度一般控制在100~200mm范圍內,對于距離長和高度大的情況,泵送一般需嚴格控制在160mm左右。
坍落度過小,會增大輸送壓力,加劇設備磨損,并導致堵管。坍落度過大,高壓下混凝土易發(fā)生離析而造成堵管。
1.2骨料的使用技術
粗骨料要符合國家現(xiàn)行標準《普通混凝土用砂、石質量標準及檢驗方法》的規(guī)定,采用連續(xù)級配,針片狀顆粒含量不宜大于10%,卵石的可泵性好于碎石。
顆粒粒徑不宜太大,粗骨料的最大粒徑與輸送管徑之比:
泵送高度在50m以下時,對碎石不宜大于1∶3,對卵石不宜大于1∶2.5;
泵送高度在50~100m時,宜在1∶3~1∶4;
泵送高度大于100m時,宜在1∶4~1∶5,
否則不宜泵送,易引起堵管。
細骨料應符合國家現(xiàn)行標準《普通混凝土用砂質量標準及檢驗方法》的規(guī)定,宜采用中砂,通過0.315mm篩孔的砂不應少于15%。
由于材料的不同,配制混凝土時砂率存在一個最佳值。砂率不宜太低,一般情況下宜采用40%~45%,大粒徑粗骨料的含量不宜過高。
合理地選擇含砂率和確定骨料級配,對提高混凝土的泵送性能和預防堵管是至關重要的。
1.3水泥用量的控制
水泥在泵送混凝土中起膠結作用和潤滑作用,水泥具有良好的裹覆性能,使混凝土在泵送過程中不易泌水,水泥的用量也存在一個最佳值,若水泥用量過少,將嚴重影響混凝土的吸入性能,同時使泵送阻力增加,混凝土的保水性變差,容易泌水、離析和發(fā)生堵管。
一般情況下混凝土中水泥的含量宜大于300kg/m3,但也不能過大,水泥用量過大,將會增加混凝土的粘性,使得混凝土失去流動性,增加泵送阻力,造成堵泵。因此,合理地確定水泥的用量,對提高混凝土的可泵性,預防堵管現(xiàn)象的發(fā)生也很重要。
1.4外加劑的選用
泵送混凝土摻用的外加劑,應符合國家現(xiàn)行標準《混凝土外加劑》、《混凝土外加劑應用技術規(guī)范》、《混凝土泵送劑》和《預拌混凝土》的有關規(guī)定。
外加劑的種類很多,應根據(jù)混凝土的強度要求和水泥的品種,合理地選擇外加劑,試配出合適的品種、合理的用量,提高混凝土的泵送性能。
1.5纖維的使用
為提高混凝土的抗裂性能,許多大體積或特殊要求的混凝土要求摻入一定量纖維(聚丙烯纖維、鋼纖維等),由于攪拌時間過短,纖維攪拌不均勻造成混凝土結塊,泵送時易造成堵泵或堵管。
因此應適當延長混凝土攪拌時間,使纖維在混凝土拌合物中均勻分布,避免結塊,減少堵泵、堵管的出現(xiàn)幾率。
1.6砂漿的配合比和用量
首次泵送時,攪拌主機、混凝土輸送車攪拌罐、料斗、管道等都要吸附一部分砂漿,用來潤滑輸送管道。正確的砂漿用量應按每200m管道需0.5m3砂漿計算,攪拌主機、料斗、混凝土輸送車攪拌罐等需0.2m3左右的砂漿。
因此泵送前一定要計算好砂漿的用量。砂漿太少易堵管,砂漿太多將影響混凝土的質量或造成不必要的浪費。砂漿的配合比也很關鍵。
當管道長度低于150m時,用1∶2的水泥砂漿;當管道長度大于150m時,用1∶1的水泥砂漿,水泥用量太少也會造成堵管。
1.7混凝土或砂漿的離析
拌制好的混凝土或砂漿再遇水時,極易造成離析,在泵送時,由于泵送壓力,漿體很快被“送走”,將骨料滯留在泵管中,沒有了漿體的潤滑作用便極易發(fā)生堵泵、堵管的現(xiàn)象。
因為砂漿與管道中的水直接接觸后,破壞了膠凝包裹層,砂漿產生離析而引起的。預防辦法是:泵前用水濕潤管道后,從管道的最低點將管道接頭松開,將余水全部放掉,或者在泵水之后,泵送砂漿之前,放入一海綿球,將砂漿與水分開,預防混凝土或砂漿的離析,阻斷了堵泵、堵管的可能性。
1.8混凝土中有異物或大結塊
混凝土中大的結塊、長形異物(如鋼筋、鐵絲等)等被吸入泵中造成堵泵或堵管。為了避免異物的誤入必須在料斗上方加設鐵篦子,發(fā)現(xiàn)異物及時清理,使混凝土順暢吸入。
泵工在作業(yè)過程中應精力集中,時刻注意泵送壓力表的示值,一旦發(fā)現(xiàn)壓力表讀數(shù)突然增大,應立即反泵2-3個行程,再正泵;
要選擇適宜的泵送速度,首次泵送時,由于管道阻力較大,此時應低速泵送,泵送正常后,可適當提高泵送速度。
當出現(xiàn)堵管征兆或某一車混凝土的塌落度較小時,應低速泵送;停機期間,對于停機時間過長,導致混凝土失水嚴重或已初凝的混凝土,不宜繼續(xù)泵送。
3.1管道連接錯誤導致的堵管
管道接法錯誤很容易導致堵管。接管時應遵循以下原則:管道布置時應按最短距離、最少彎頭和最大彎頭來布管,盡量減小輸送阻力,也就減少了堵管的可能性。
泵出口錐管處,不許直接接彎管,至少應接入5mm以上直管后,再接彎管。
泵送中途接管時,每次只能加接一根,且應用水潤滑一下管道內壁,并排盡空氣,否則極易造成堵管。垂直向下的管路,出口處應裝設防離析裝置,預防堵管。
高層泵送時,水平管路的長度一般應不小于垂直管路長度的15%,且應在水平管路中接入管路截止閥。停機時間超過5min時,應關閉截止閥,防止混凝土倒流,導致堵管。由水平轉垂直時的90°彎管,彎曲半徑應大于500mm。
3.2設備局部漏漿造成的堵管
由于砂漿泄漏掉,一方面影響混凝土的質量,另一方面漏漿后,將導致混凝土的塌落度減小和泵送壓力的損失,從而導致堵管。漏漿的原因主要有以下幾種:
輸送管道接頭密封不嚴;眼鏡板和切割環(huán)之間的間隙過大;混凝土活塞磨損嚴重;因混凝土輸送缸嚴重磨損而引起的漏漿。
3.3攪拌車攪拌葉片損壞
當采用攪拌車運送混凝土時,由于攪拌車滾筒內攪拌葉片磨損造成部分粗集料下沉到底部,在泵送到此部分混凝土時,混凝土中粗集料過多,易發(fā)生堵泵或堵管。
因此攪拌站應制定檢查攪拌設備制度,對罐車攪拌葉片定期進行檢查,磨損嚴重時要及時更換。
夏季混凝土施工容易失水。環(huán)境溫度達到32℃以上時,因太陽光直射,輸送管管壁溫度最高可達70℃以上,加速了混凝土的失水,容易造成堵泵;
冬季大氣溫度較低混凝土易受凍結冰致使堵泵,因此在北方地區(qū)更要加強冬施設備的保溫工作,確?;炷猎诳杀脿顟B(tài)下作業(yè)。
作為半成品的預拌混凝土,在泵送過程中引起堵泵、堵管的原因是多方面的,從業(yè)人士應從原材料的選用、配合比、泵工的操作水平、機械設備等方面著手,在每一次施工中積累經驗,抓好每一個環(huán)節(jié),從而降低堵泵發(fā)生的概率,真正提高泵送施工的效率。